Selective Laser Sintering (SLS)
Beispiel SLS-Druckprozess
Details SLS-Druck
Beim SLS wird Kunststoffpulver in einen absenkbaren Bauraum gefüllt und über einen Laserstrahl selektiv erhitzt und lokal sowie schichtweise versintert.
Das Verfahren wird nach DIN EIN ISO/ASTM 52900 in die Prozesskategorie Powder Bed Fusion (PBF) eingeordnet. Neben dem SLS zählen auch noch das Selective Laser Melting (SLM) und das Electron Beam Melting (EBM) in diese Kategorie.
Zu beachten ist, dass bei SLS in der Regel Kunststoffpulver genutzt wird und bei SLM sowie EBM Metallpulver.
Das Verfahren ist aufwendiger als FDM und insgesamt von den Geräte- und Prozesskosten auch teurer. Es wurde Mitte der 1980 Jahre entwickelt und ist heute gerade im industriellen Umfeld verbreitet.
Mit SLS lassen sich mechanisch gut belastbare Bauteile herstellen.
Das Material beim SLS ist Kunststoffpulver. Die gebräuchlichsten Pulver bestehen aus Nylon bzw. PA, PP und TPU. Mit Additiven gefüllte oder ungefüllte PA12- und PA11-Pulver werden häufig verwendet.
- Anspruchsvolle funktionale Prototypen
- Endprodukte
- Kundenspezifische Konsumprodukte
- Ersatzteile
- Chirurgiemodelle und Werkzeuge
- Werkzeuge
- Leitungen und Halterungen
- Giveaways
- Fahrradkomponenten
- Prothese
- Medizinische Modelle
Bilder findet ihr hier auf Pinterest.
Prozesseigenschaften beim SLS
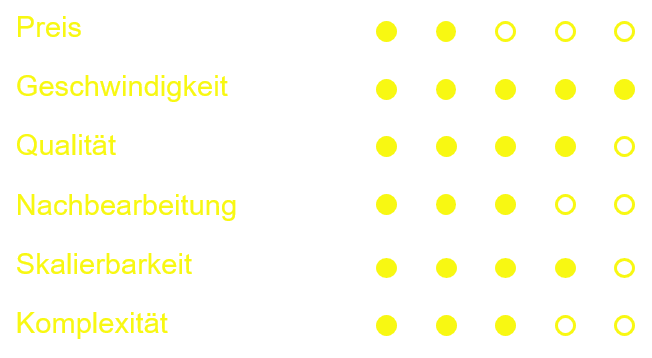
Mechanische Eigenschaften SLS-Bauteile
Festigkeit ist die Fähigkeit, mechanischer Belastung standzuhalten, ohne zu versagen.
Bei SLS-gedruckten Bauteilen kann die Festigkeit sehr hoch sein. Sie kann sogar häufig nah an die Eigenschaften von spritzgegossenen Kunststoffteilen herankommen. Die genaue Festigkeit hängt dabei immer von verschiedenen Faktoren ab, darunter das verwendete Material, die Druckparameter und die Nachbearbeitung.
Steifigkeit beschreibt die Widerstandsfähigkeit eines Materials gegen Verformung unter einer angewandten Last.
SLS-gedruckte Bauteile haben eine relativ hohe Steifigkeit im Vergleich zu anderen 3D-Druckverfahren, da die Pulverpartikel durch den Lasersinterprozess gut miteinander verschmelzen und eine gleichmäßige Struktur bilden.
Zähigkeit ist die Fähigkeit eines Materials, Energie zu absorbieren, bevor es versagt.
SLS-gedruckte Teile haben eine gute Zähigkeit, besonders im Vergleich zu FDM, da die mechanischen Eigenschaften in alle Richtungen gleich (isotrop) sind. Zugleich sind die Bauteile noch belastbar, sodass sie Stößen und Verformungen standhalten können.
Die Schlagfestigkeit bezieht sich auf die Fähigkeit eines Materials, Stoßbelastungen zu widerstehen, ohne zu brechen oder zu versagen.
Die Schlagfestigkeit von SLS-Bauteilen ist meist gut und reicht für mechanisch belastbare Anwendungen aus. Sie variiert aber je nach Material.
Die Bruchdehnung gibt an, wie weit ein Material unter Zugbelastung gedehnt werden kann, bevor es versagt.
Die Bruchdehnung ist beim SLS stark vom Material und der Anwendung abhängig. PA12 weist eine moderate Bruchdehnung von 10 bis 25 % auf, flexibles TPU bspw. eine deutlich höhere.
Die Reaktion eines Materials auf chemische Einflüsse kann seine mechanischen Eigenschaften beeinträchtigen.
SLS-gedruckte Teile haben eine gute chemische Beständigkeit gegenüber Ölen, Fetten, Alkalien und vielen Kohlenwasserstoffen, sind jedoch anfällig gegenüber starken Säuren und einigen Lösungsmitteln.
Materialkennwerte SLS
Polyamid 12
> Zugfestigkeit: 45-55 MPa
> Biegefestigkeit: 60-70 MPa
> Elastizitätsmodul: 1,5-1,8 GPa
> Schlagfestigkeit: 4-6 kJ/m²
> Verformungstemperatur bei 0,45 MPa: 90-100 °C
Polyamid glasfaserverstärkt
> Zugfestigkeit: 60-85 MPa
> Biegefestigkeit: 90-120 MPa
Elastizitätsmodul: 3-6 GPa
Schlagfestigkeit: 2-4 kJ/m²
Verformungstemperatur bei 0,45 MPa: 170-190 °C
Polyamid 11 (biobasiert)
> Zugfestigkeit: 45-55 MPa
> Biegefestigkeit: 55-65 MPa
Elastizitätsmodul: 1,5-1,9 GPa
Schlagfestigkeit: 5-10 kJ/m²
Verformungstemperatur bei 0,45 MPa: 95-105 °C
Polypropylene
> Zugfestigkeit: 20-30 MPa
> Biegefestigkeit: 25-35 MPa
Elastizitätsmodul: 1-1,5 GPa
Schlagfestigkeit: 5-12 kJ/m²
Verformungstemperatur bei 0,45 MPa: 80-100 °C
Thermoplastische Polyrurethane
> Zugfestigkeit: 8-25 MPa
> Reißdehnung: 200-700 %
Elastizitätsmodul: 0,01-0,08 GPa
Schlagfestigkeit: ca. 50 kJ/m²
Verformungstemperatur bei 0,45 MPa: 60-80 °C
Vorteile
- Vielseitigkeit bei den Materialien
- Hohe Festigkeit und Stabilität
- Gute mechanische Eigenschaften
- Detailgenauigkeit
- keine Stützstrukturen notwendig
- Wirtschaftlichkeit bei Kleinserien
- Widerstandsfähigkeit gegen Chemikalien und Hitze
Nachteile
- Hohe Anschaffungs- und Betriebskosten
- Teure Materialien
- aufwendige Nachbearbeitung
- rauhe Oberflächen
- Schutz vor Staubenwicklung