Fused Deposition Modeling (FDM)
Beispiel FDM-Druckprozess
Details FDM-Druck
Beim FDM wird ein Materialfaden in einem Extruder erhitzt und über eine Düse schichtweise auf eine Druckplattform aufgetragen.
Das Verfahren wird nach DIN EIN ISO/ASTM 52900 als Material Extrusion (MEX) bezeichnet.
Bekannte Markennamen sind auch FDM, FFF und FLM.
Das Verfahren ist relativ einfach und kostengünstig. Es wurde bereits 1980 entwickelt und ist heute das am weitesten verbreitete 3D-Druckverfahren.
Das Material beim FDM wird als Filament bezeichnet. Die gebräuchlichsten Filamente bestehen aus den Thermoplasten PLA, ABS und PETG. Es gibt jedoch noch viele weitere Spezialmaterialien wie TPU, Nylon, CFK bis hin zu PEEK.
Eine Besonderheit stellt wasserlösliches PVA dar, welches beim FDM häufig als auswaschbares Supportmaterial dient.
- Prototypenbau, funktionale Modelle und Kleinserienbauteile
- Individuelle Werkzeuge, Aufsätze und komplexe Formen
- Individualisierte medizinische Prothesen, Orthesen und Implantate
- Architektur- und Designmodelle
- Technische Bauteile, z. B. für die Luft-und Raumfahrtindustrie
- Werkzeuge
- Technische Bauteile und Kleinserien
- Giveaways
- Lampen, Halterungen
- Vasen, Töpfe
- Deko
Bilder findet ihr hier auf Pinterest.
Prozesseigenschaften beim FDM
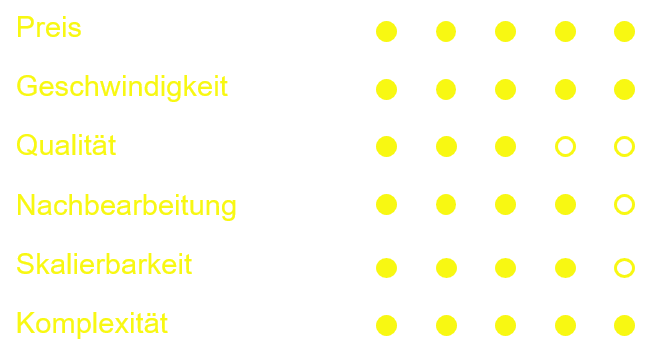
Mechanische Eigenschaften FDM-Bauteile
Festigkeit ist die Fähigkeit, mechanischer Belastung standzuhalten, ohne zu versagen.
FDM-gedruckte Teile haben in der Regel nicht die gleiche Festigkeit wie Spritzgussteile. Durch geeignete Materialauswahl, Druckparameter und Designoptimierung können aber auch hochfeste FDM-Teile hergestellt werden.
Steifigkeit beschreibt die Widerstandsfähigkeit eines Materials gegen Verformung unter einer angewandten Last.
FDM-Drucke neigen dazu, im Vergleich bspw. zu spritzgegossenen Teilen weniger steif zu sein, insbesondere bei dünnen Wänden oder bei Verwendung von Füllstrukturen mit geringer Dichte.
Zähigkeit ist die Fähigkeit eines Materials, Energie zu absorbieren, bevor es versagt.
FDM-gedruckte Teile können im Allgemeinen zäh sein, insbesondere wenn hochschlagzähe Materialien wie ABS oder Nylon verwendet werden.
Die Schlagfestigkeit bezieht sich auf die Fähigkeit eines Materials, Stoßbelastungen zu widerstehen, ohne zu brechen oder zu versagen.
Materialien wie ABS und ASA bieten eine gute Schlagfestigkeit bei FDM-Drucken.
Die Bruchdehnung gibt an, wie weit ein Material unter Zugbelastung gedehnt werden kann, bevor es versagt.
Einige Materialien wie TPU (thermoplastisches Polyurethan) bieten eine hohe Bruchdehnung und eignen sich gut für flexible Anwendungen.
Die Reaktion eines Materials auf chemische Einflüsse kann seine mechanischen Eigenschaften beeinträchtigen.
Materialien wie PETG und ABS bieten eine gute Beständigkeit gegenüber vielen Chemikalien.
Materialkennwerte FDM
Polylactide
> Zugfestigkeit: 60-70 MPa
> Biegefestigkeit: 60-70 MPa
> Elastizitätsmodul: 2-4 GPa
> Schlagfestigkeit: 5-10 kJ/m²
> Verformungstemperatur bei 0,45 MPa: 50-60 °C
Acrylnitril-Butadien-Styrol
> Zugfestigkeit: 40-50 MPa
> Biegefestigkeit: 40-50 MPa
Elastizitätsmodul: 2-3 GPa
Schlagfestigkeit: 10-30 kJ/m²
Verformungstemperatur bei 0,45 MPa: 80-100 °C
Polyethylenterephthalat
> Zugfestigkeit: 40-60 MPa
> Biegefestigkeit: 50-75 MPa
Elastizitätsmodul: 1,8-2,2 GPa
Schlagfestigkeit: 5-12 kJ/m²
Verformungstemperatur bei 0,45 MPa: 70-80 °C
Polyamid/ Nylon
> Zugfestigkeit: 50-80 MPa
> Biegefestigkeit: 60-100 MPa
Elastizitätsmodul: 1-1,8 GPa
Schlagfestigkeit: 10-15 kJ/m²
Verformungstemperatur bei 0,45 MPa: 75-90 °C
Thermoplastische Polyrurethane
> Zugfestigkeit: 25-70 MPa
> Reißdehnung: 300-600 %
Elastizitätsmodul: 0,01-0,05 GPa
Schlagfestigkeit: >50 kJ/m²
Verformungstemperatur bei 0,45 MPa: 40-60 °C
Polyetheretherketon
> Zugfestigkeit: 90-100 MPa
> Biegefestigkeit: 120-150 MPa
Elastizitätsmodul: 3,5-4 GPa
Schlagfestigkeit: 5-15 kJ/m²
Verformungstemperatur bei 0,45 MPa: 150-165 °C
Vorteile
- Erschwinglichkeit
- Vielseitigkeit bei den Materialien
- Einfachheit und Benutzerfreundlichkeit
- Skalierbarkeit bei der Druckgröße
- Belastbare und funktionale Bauteile
- Große Community und Unterstützung
Nachteile
- Geringere Detailgenauigkeit
- Relativ langsame Druckgeschwindigkeit
- Anisotropie und mechanische Schwäche
- Warping und Verzug
- Stützstrukturen und Nachbearbeitung
- Schlechte Oberflächenqualität und Maßhaltigkeit